10 Lean Principles to Improve Your Business Operations
By Oyama James on September, 19 2024 | Views: 3772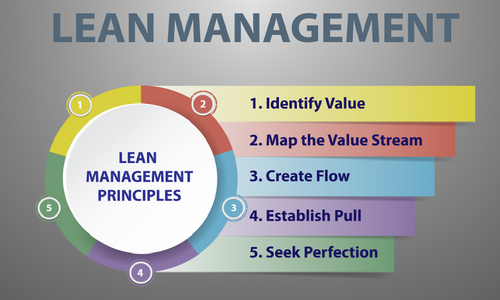
Lean principles focus on maximizing value while minimizing waste in business operations. Implementing lean principles can help businesses streamline operations, enhance customer satisfaction, and boost profitability Here are some key lean principles that can help improve your business operations:
1. Identify Value
- Determine what constitutes value from your customers’ perspective. Understand their needs and expectations to deliver products or services that meet or exceed them.
2. Map the Value Stream
- Examine the flow of materials and information in your processes. Create a visual representation (value stream map) to identify and eliminate non-value-added activities (waste).
3. Create Flow
- Ensure a smooth and continuous work flow throughout your operations. This can involve organizing workstations, minimizing delays, and optimizing layout for a seamless transition between steps.
4. Establish a Pull System
- Implement a pull system where production is driven by actual customer demand rather than forecasts. This approach helps to reduce overproduction, lower inventory levels, and align production with real customer needs.
5. Aim for Perfection
- Cultivate a culture of continuous improvement (Kaizen) where employees are encouraged to identify inefficiencies and propose solutions. Regularly review processes to pursue incremental enhancements.
6. Empower Your Workforce
- Engage and empower employees by involving them in decision-making. Provide training and resources to help them identify inefficiencies and contribute to operational improvements.
7. Standardize Processes
- Develop standardized work procedures to ensure consistency and efficiency. Document best practices and encourage adherence to these standards while allowing for ongoing improvements.
8. Prioritize Quality
- Implement quality control measures throughout the production process. Focus on preventing defects rather than detecting them, which reduces waste associated with rework and returns.
9. Optimize Inventory Levels
- Minimize excess inventory by adopting just-in-time (JIT) practices. This strategy reduces holding costs, lowers the risk of obsolescence, and frees up capital for other uses.
10. Leverage Data for Decision-Making
- Use data analytics to inform decisions and monitor performance. Implement key performance indicators (KPIs) to track progress and make informed adjustments for continuous improvement
Source APGEE BLOG NEWS
Posted November, 5 2019
You may also like...
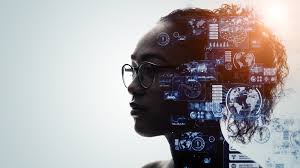

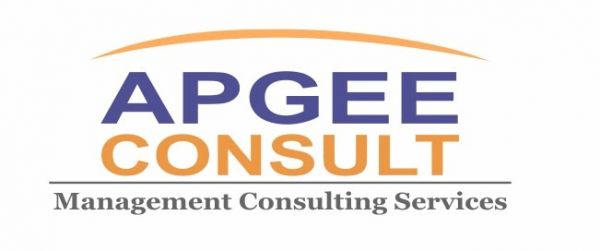